By Jay Palter | May 3, 2023
The manufacturing sector is in the midst of transforming into Industry 4.0. Information technology saturates every corner of our production, administration, and safety operations. But not all technology is created equal.
What is worth investing in, and what is best left by the wayside? One of the most flexible and reliable services you can use is RFID wireless tracking. It is adaptable to a wide range of use cases and works in practically any manufacturing facility.
Is RFID the right solution for your plant or warehouse? This article explains what RFID is, how RFID tracking can help your business, and how RFID technology in manufacturing is effectively used today.
Download our guide and learn more:
[Download] Best Practices for Equipment Management in Distribution Centers
What is Radio Frequency Identification (RFID)?
RFID stands for radio frequency identification, a short-range wireless communication standard commonly used for tracking purposes in manufacturing facilities and warehouses. RFID tags securely transmit their identity and other important data when placed close to scanners—for example, in the consumer world, with tap-to-pay credit cards.
RFID technology in manufacturing is a good choice for asset tracking because it doesn’t conflict with other common business wireless standards. For example, WiFi internet and two-way radios work perfectly fine alongside RFID.
It offers other important benefits too. For example, RFID technology in manufacturing doesn’t require line-of-sight. Signals can pass through wood, plastic, and other common building materials. Scanners can read separate tags inside a scanned toolkit, hard case, or other containers. However, it is important to know that metal reflects RFID signals, so it might not be the best choice in some facilities with many walled metal surfaces.
How Do Warehouse and Manufacturing RFID Key and Asset Tracking Systems Work?
RFID tracking systems are powerful, flexible technologies that manufacturers and shipping and distribution centers can easily customize to the ways they work. They fit neatly into lean manufacturing technology practices by automating and enforcing tight process control over what are otherwise tedious manual tasks.
While installations will differ between facilities with different use cases, RFID tracking systems are always built from a few essential core components: storage cabinets, RFID tags, readers and access terminals, and management software.
Storage Cabinets
RFID tracking systems may be advanced, smart technology, but they must still be built on top of secure, reliable storage cabinets. These hold keys, handheld scanners, toolkits, and other important equipment when those assets aren’t used. In addition, cabinets often include charging ports to ready electronic devices and data cables for fault monitoring.
Advanced tracking system cabinets are modular, meaning you can stack and configure them for different floor plans and use cases. For example, a manufacturing facility may want to track maintenance toolkits and expensive mechanical calibration tools of all different shapes and sizes. Whereas a warehouse may want to charge and ready rows upon rows of identical handheld scanners.
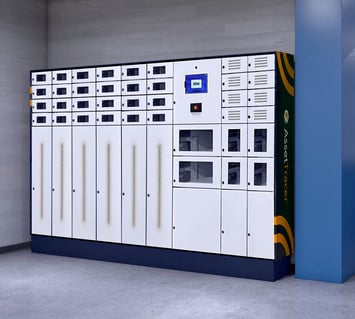
RFID Tags
RFID tags power modern tracking systems. Manufacturing facilities use a combination of passive and active RFID tags. Passive tags do not have an onboard battery. Think of the small RFID chips embedded in credit cards. They transmit their identity when someone brings them close to an RFID reader on the exterior of a storage cabinet or distributed throughout your facility.
Active-powered RFID tags with a built-in battery are also available. They have a greater range but are also bulkier and more expensive, making them suitable only for RFID in supply chain management, especially high-value products as they move down your production line.
The tags are usually attached to or embedded in equipment in manufacturing tracking systems. For keys, that typically takes the form of an RFID fob attached to the key ring that doubles as the locking mechanism in the storage cabinet. Tagging varies much more with equipment and kit items. Some electronics, like radios, mobile devices, and handheld scanners, come with embedded RFID tags or a fob slot where you can add one. With other equipment, you need to attach the tag to the exterior.
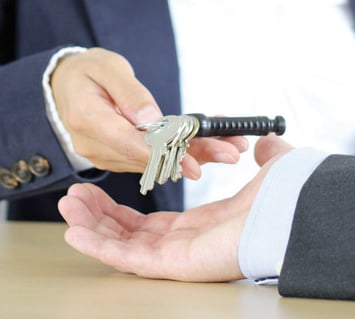
RFID Readers
RFID readers emit a harmless radio signal that bounces off nearby RFID tags when they’re in range. That returns identity data the reader can analyze to track the tagged item’s location and use. These scans take a fraction of a second, and readers can scan multiple tags simultaneously. Most warehouse and manufacturing RFID tracking systems will have a reader mounted on or near the storage cabinets so your staff can scan items as they take or return them.
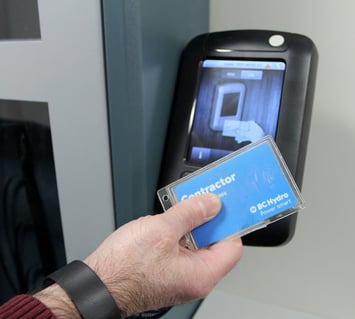
Access Terminals
The access terminal on the front of the storage cabinet is your staff’s primary interface with the RFID tracking system. Users authenticate themselves at the terminal when they want to sign out or return a stored item. In addition, access terminals can utilize one more access control method, such as swipe cards, PIN codes, or biometrics, such as fingerprint, iris eye scan, or facial recognition, for controlling access to especially-important assets.
Advanced tracking systems use touchscreens for access terminals to provide customized checklists. This is one of the key ways RFID in manufacturing can improve process controls. For example, when a technician signs out instruments to repair production equipment, you can prompt them to verify that it is properly calibrated. If they don’t answer, the technician’s supervisor receives an immediate email warning them that the equipment may not be properly repaired. This helps you avoid costly downtime and rework.
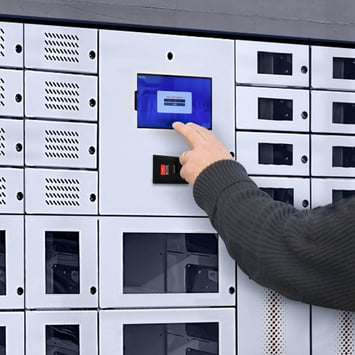
Management Software
Data from the RFID readers, cabinets, and access terminal all flow back to a software management dashboard that production supervisors use to get real-time tracking data on RFID-tagged equipment and keys. Modern software dashboards are designed as web apps. So they’re accessible from any company device, like authorized desktop computers in the plant office or smartphones and tablets down on the floor.
Through the dashboard, your supervisors can receive real-time tracking alerts if keys or equipment are overdue for return. Your supervisors can also generate reports that show them detailed tracking histories so they can help identify meaningful trends you might not see otherwise. That helps you monitor employee performance, ensure accountability, and improve compliance with important industry standards and management best practices.
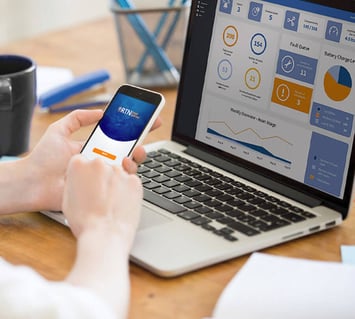
How Can RFID Tracking Systems Help Manufacturing and Warehouse Operations?
RFID tracking systems improve operations in many important ways.
Standardize essential workflows for better Lean Management
Smart key and asset tracking systems do more than just monitor the physical materials they store. They offer important insights into the workflows within which those items are used. Better tracking will help you automate and standardize important processes so that work is carried out consistently, reliably, and with good feedback when errors occur. For example, you’ll know immediately if any production floor staff start their shifts without essential equipment and toolkits.
Generate new process efficiencies
Your efficiency rates will increase when you know precisely where vital keys, equipment, and mobile devices are at any time, who signed them out, and when they’re due for return. You won’t waste time hunting for missing equipment. You’ll maintain peak asset utilization.
They reduce costs
RFID warehouse equipment tracking systems for manufacturing facilities and warehouses can save your staff hours of labor every week by automating tedious, manual equipment and key management. The RFID tracking system will automatically compile everything. Those hours will quickly add up and offset the upfront costs of an RFID tracking system. That is before any operating efficiencies you’ll gain. For example, managers won’t spend as much time overseeing asset transactions and monitoring reports.
Improve employee accountability
Every transaction your production, maintenance, or service staff make is tracked. The tracking systems enforce better accountability among staff signing keys and equipment in or out. They also record the condition of everything signed out. Is it fully charged? Did the user report any fault codes or other issues with the device?
Automating equipment and key management also reduces the opportunities for staff to lose critical assets. For example, suppose a staff member is ever late returning important equipment. In that case, the system can send an immediate alert to supervisors so they can track it down and get it returned to circulation.
Use Cases for RFID Tracking Systems at Manufacturing Facilities & Warehouses
Facility and fleet key tracking
RFID tracking systems never tire at the end of a shift, call out sick, or make human errors because they’re rushing. Instead, everything is tracked and accounted for every time a staff member uses it.
They’re a great tool for managing facility and vehicle key transactions, so you always have an airtight record of who took the keys and when they’re due for return. Important, regulated processes won’t ever be delayed because staff members are trying to hunt down who has a key for a lift or to your manufacturing cold room.
See how strong RFID keyfobs can be (Video)
Handheld device tracking
Modern manufacturing and shipping centers rely on staff using handheld scanners to track everything moving in and out of the facility. Pallets, individual boxes, individual picked items. They’re complex places, and leaving staff without functional scanners isn’t an option. Scanners must be charged and available for every staff member at the start of every shift.
Learn More: See Best Practices for Managing Warehouse Scanners
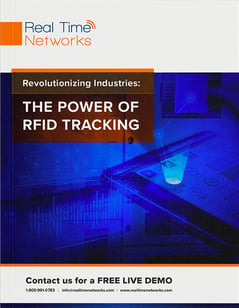
Discover the Power of RFID
See how RFID tracking systems work, how they’re used in industry today, and some best practices for adapting them to your organization’s workflows.
Subscribe to our blog
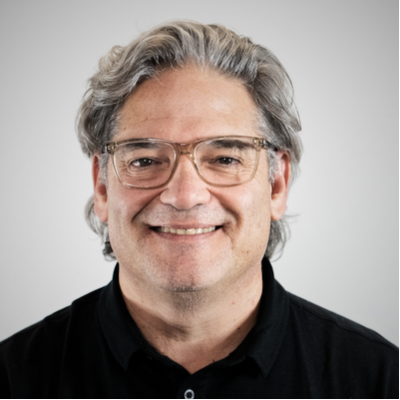
Jay Palter
Vice President of Marketing & Partnerships