By Jay Palter | April 12, 2022
Everyone wants to do more with less. But in business, finding reliable ways to do more is easier said than done. Entire consulting industries have risen based on the shaky promise of finding those types of solutions. Do solutions really exist?
Lean is defined as a set of management practices to improve efficiency and effectiveness by eliminating waste. The core principle of lean is to reduce and eliminate non-value adding activities and waste. It has its origins in manufacturing, but today lean thinking is a wildly popular approach for optimizing operations in any business setting.
This article explains how lean thinking and Real Time Networks' secure asset management and safety products can help your organization eliminate waste and operate more efficiently. First, we focus on the 7 categories of waste, and second, we highlight how lean thinking have helped our customers streamline operations by eliminating inefficient or ineffective processes.
Lean Methodology Aims to Remove Waste and Reduce Variance
Lean thinking focuses on optimizing business processes, specifically identifying and removing waste and eliminating variance in how your people and systems carry out those processes. In addition, it focuses on finding any opportunities for process improvement, especially through automation.
Lean thinking is not intended to be a one-time activity. Instead, lean is intended to become a part of a company’s culture where it seeks to make continuous improvements to every process it carries out.
"Lean waste" is any activity in a business process that does not directly lead to value being created for a customer. To eliminate lean waste, businesses following a lean methodology seek to get the right resources to the right places at the right time.
Lean originated in Japanese manufacturing
The core ideas behind lean thinking originated in the Toyota Production System, which Toyota engineers and executives developed between 1948 and 1975. The company published its first official descriptions of the System in the 1990s. Adoption spread rapidly from there, evolving into the lean methodology we know today.
The 7 Wastes of Lean Manufacturing
Taiichi Ohno, father of the Toyota Production System (TPS), defined three categories of waste: mura (unevenness), muri (overburden), and muda (waste). The purpose of lean manufacturing is to find and eliminate muda, mura, and muri, to improve quality, safety, and efficiency.
- Muda - Any activity that consumes resources without creating value for the customer
- Mura - Unevenness in an operation
- Muri - Overburdening equipment or operators by requiring them to run at a higher or harder pace with more force and effort for a longer period of time than equipment designs and appropriate workforce management allow.
There are 7 types of waste in lean manufacturing: transportation, inventory, motion, waiting, overproduction, overprocessing, and defects.
Transportation
Each of the 7 wastes of lean is shorthand for specific business processes. For example, under lean, transportation waste refers to the movement of your product or the resources used in its production.
Every time your business moves a resource, it introduces the risk of that resource getting damaged, lost, or simply delayed in reaching its destination. Once you identify a transportation waste, the improvement you must make is often either a change to your worksite that eliminates the need to move as much or a change in process that eliminates the need for transportation entirely.
Inventory
Inventory waste is a bottleneck. This waste occurs when you have excess material waiting to be processed. Since that material isn’t ready to be sold to a customer, it represents an outlay of capital that is sitting idle. It has to be counted and safeguarged.
Lean thinking looks to reduce the volume of idle inventory as much as possible. But of course, depending on your work environment, it might be impossible to eliminate inventory waste completely, but a lean organization will seek to minimize it.
Motion
Whereas transportation waste occurs when your product and its constituent materials move, motion waste occurs when your employees or production systems make an unnecessary movement. For example, every time a worker moves, they increase fatigue and their risk of injury. Or every time a system makes an unnecessary movement that increases the chance of wear or damage.
Waiting
Under lean, unnecessary idling time is called the waste of waiting. This applies to your people or your production systems like with motion waste. If it is sitting idle waiting to do work, it is wasted.
Waiting waste often occurs due to a lack of coordination among your different operating units. But it can also appear when your business processes are unreliable when attempting to batch work unnecessarily or during uncoordinated shift changes.
Overproduction
Overproduction is what most people think of when they think of “waste.” This is when you produce too much of a product or service, or produce it at the wrong time.
You can just as likely overproduce a digital asset as you could a physical one. For example, if you have an automated management system sending nightly reports that go unread because readers don’t see value in them, you’re overproducing reports.
You can eliminate overproduction waste through better planning and forecasting. To do that, you need good data to know how much of a given product or service is needed at which time and in which location.
Overprocessing
Overprocessing—or overbuilding—is when your employees or systems spend resources to make a product or service past the point at which a customer values it and is willing to pay for it. Overprocessing waste can occur when your employees are not properly trained, or your understanding of customer needs is off-target.
It is obviously important for your organization to provide quality products and services, but it is equally important to know when enough is enough, and devoting more time and resources would be wasteful. As with many other lean wastes here, identifying that tipping point requires good data.
Defects
Defects of waste arise when a product or service must be remanufactured, repaired, or rescheduled. You can waste a great deal of time and effort thanks to even small errors in production.
To eliminate the need for repairs or reprocessing, you need to identify the root cause of the defect. Was it human error? Improper training? A miscalibrated system? That's the process you need to address.
Lean Business Use Cases for RTN Products
Real Time Networks produces various management and safety solutions that help you protect your people, assets, and keys. They’re networked and automated, making them ideal support tools for organizations looking to foster a lean culture.
Here are just some of the most recent examples of RTN customers in different sectors using our products to support their lean business practices.
Warehouses & Distribution
Staff use handheld scanners constantly in shipping and distribution centers. Having a working scanner on hand is so important for warehouse workers that at one Real Time Networks’ customer location, workers would regularly hide their favorite known-working scanners around the warehouse.
This problem became so acute that management completely lost track of how many scanners they owned. They had a waste of inventory – too many resources purchased and going unused.
They purchased an AssetTracer system that could manage the tracking and distribution of all of their scanners at the beginning and end of shifts. If staff didn’t return a scanner on time, the supervisor would receive a report with the user's identity who signed it out so the supervisor could immediately investigate the problem. As a result of eliminating the scanner hoarding, this company discovered they needed 15-20% less devices than they had previously.
Optimize your warehouse management with our guide:
[Download] Best Practices for Equipment Management in Distribution Centers
Law Enforcement
Police officers rely on a large amount of equipment to keep themselves and the public safe. Some of that kit they maintain themselves, other kit they must sign out from an equipment manager at the start of their shift. In a busy precinct, it can take each officer several minutes every day to get what they need. Multiply that time by every officer, every shift over a year, and you have a significant waiting waste.
KeyTracer and AssetTracer systems have easy-to-use automated access terminals. As a result, officers at many customer agencies can sign out all of the gear they need in seconds to get on the road fast.
Hospitality & Gaming
In the last few years, more and more hotels have sought better process control over housekeeping operations to maximize how efficiently they could get guests into their rooms. They had a waste of waiting and also a waste of defects. If a housekeeper needed to be pulled away from one task to handle an urgent room turnover, they would need to reschedule and redo other work.
To combat these wastes, hotels now provision tablets to housekeepers to provide up-to-the-second insights on room turnover progress. Frontdesk staff can monitor in real time when rooms are ready.
However, all of those tablets require management and storage. As a result, many hotels and other hospitality venues have turned to Real Time Networks for automated asset storage solutions for their tablets and mobile devices.
Fleet Management
The City of Saint John, New Brunswick, recently deployed a KeyTracer system to help manage their newly centralized vehicle fleet. Their fleet manager had discovered vehicles of a certain class were drastically underutilized. As a result, they had a waste of inventory and a waste of transportation, with excessive damage from vehicle use raising maintenance costs. The KeyTracer system allowed the City to save over $150,000 per year in vehicle costs, while maintaining a smaller, remotely-managed pool of passenger vehicles without compromising availability.
Real Time Networks’ management and safety solutions may be just the tools you need if you're looking to develop a lean culture at your workplace.
Subscribe to our blog
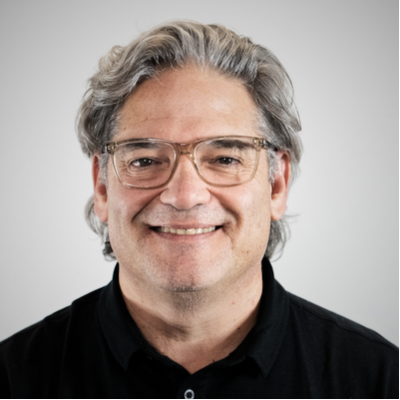
Jay Palter
Vice President of Marketing & Partnerships