By Jay Palter | May 5, 2022
Lean methodologies are ways of organizing and improving how we work. Different lean thinking variations exist, but they all share the same core goals:
- To generate more value for customers
- To eliminate waste from individual and organizational processes
- And to create a self-reinforcing feedback loop of continuous improvement
Those goals can sound simple—almost too simple like they’re nothing more than common sense. In a way, that is true. You can think of lean methodologies as “advanced common sense” for businesses and other large organizations.
Lean ideas are straightforward. The challenge is execution. Lean companies need to stick with that way of doing business, with the right tools, across their organization. That requires trusted systems and tools.
One tool many organizations would benefit from including in their lean practice is a smart equipment management system. This article explores how equipment management can improve your lean performance. It also offers one example of a Real Time Networks enterprise customer who transformed how its shipping and logistics teams operated thanks to an AssetTracer equipment management system.
How Lean Can Benefit Any Organization
Many people know that lean thinking originated in the manufacturing sector, specifically at Toyota. And while lean has a lot to offer manufacturing businesses, the core principles are well-suited to improve any company.
Lean isn’t about building a better widget when you boil it down. Instead, it is about process control—improving the reliability, efficiency, and value of your organization's processes.
Lean methodologies are not a quick fix to hit monthly or quarterly KPIs. Proper implementation requires a strategic, longer-term perspective on what is best for a business and its customers.
What are Smart Equipment Lockers?
A regular storage locker has one job: secure equipment. It doesn’t need to do more or less. That may seem like an efficient function, but the evolution of “smart technology” has changed that perception in the last several decades.
Smart technology is traditional business equipment embedded with a computer monitoring system. These systems track when equipment is taken or returned and even how it is used. A smart equipment management system can automate all of these time-consuming tasks. In addition, the systems are so adaptable that they enable new processes and management activities that support lean business functions.
Several core components are needed to make a locker system “smart.”
The storage lockers
The storage locker is the secure storage space for your equipment. Depending on the business system you purchase, the storage lockers might be one-size-fits-all cabinets or stackable, modular compartments you can mix and match for your specific needs.
Real Time Networks deploys modular lockers that are a more efficient use of your floor space. That also makes them easier to adapt to any work site so that you can position them as close as possible to their point of use.
Content surveillance
Storage lockers can be more than bare metal. They can include powerful content surveillance tools, which are monitoring tools built into storage compartments.
For example, wired USB connections can monitor the health of electronic devices. Wireless RFID tags can verify the identity of each item taken or returned, so a user can’t accidentally or maliciously report one item returned but deposit another. If the surveillance system detects an anomaly, it can notify the user right at the locker or remotely alert managers and security of serious issues.
Smart access control panels
Users authenticate themselves at networked access control panels to sign equipment in or out. They could use various authentication methods, including RFID tokens, swipe cards, PIN codes in lower security environments, or contactless biometrics.
You can also use smart panels to present customized checklists or other prompts when a user interacts with the locker system. For example, you can require users to return consumable materials to confirm whether any item is running low.
Smart tags
Content surveillance and access control features depend on knowing which assets are in storage compartments. RFID is the most common wireless standard for smart tags. Radiofrequency identification (RFID) is a short-range, wireless standard commonly used for machine-to-machine communication.
Management software
Smart technology generates a great deal of value through automation. But it also offers value by generating large volumes of business intelligence from its network of monitoring tools.
The central management software in a smart equipment management system compiles insightful reports from this data. They also support tighter process control so that you know how workflows involving equipment transactions are progressing end-to-end.
How Better Equipment Management Supports Lean
At a high level, process control is what an equipment management system does best to support lean thinking. But the details matter here. Better equipment management supports lean businesses in five specific ways.
-
Centralization
Centralization is a key tenet of lean thinking. To increase efficiency, you need to reduce variance among all of the distributed worksites where you need to manage equipment.
Smart lockers are networked, which means you can control access and monitor the performance of any number of distributed lockers around your worksite through the management dashboard.
-
Automation
Under lean, you want to use automation to simplify and streamline complex processes, so you reduce waste and errors. Equipment management is one such complex process.
-
Recordkeeping
Creating a continuous improvement cycle within your organization requires understanding what has happened in the past and what’s happening right now throughout your corporate ecosystem. That understanding requires detailed recordkeeping.
A smart equipment management system provides better recordkeeping, enabling you to set better benchmarks, track performance against your KPIs, and analyze results. Electronic recordkeeping reduces waste and generates insights more efficiently, too.
-
Accountability
Applying lean thinking requires some careful leadership. It’s not a top-down enforced set of practices. It’s an end-to-end program for process control, which means you need buy-in and support from every level of your organization. Lean needs accountability and transparency to work. Everyone, from the CEO to the equipment manager, to staff members signing assets in or out, have roles and responsibilities they need to follow.
-
Trust
Accountability leads to trust. Lean thinking requires everyone to be pulling in the same direction, which means everyone needs to understand that the organization's process improvements under lean are for everyone’s benefit. They need to trust the system.
Use Case: Trustworthy Warehouse Scanner Tracking
Let’s consider an example. Real Time Networks worked with an enterprise customer in the clothing business. They manufactured and shipped their products internationally and had some of the busiest warehouses in North America.
Their workers used handheld scanners to inventory and track the different materials and pallets passing through their warehouses. Rows upon rows of scanners were lined up next to warehouse timeclocks. An employee would punch in, grab a scanner, hope it was in working order, and try to go about their day without the scanner erroring out or running out of power.
The problem with scanners
Nothing could happen in this company’s warehouse without the scanner, and the employees knew it. But since there was no system to manage the signout or return of scanners, there was no process to verify they were charged and working or even that there were enough to go around. So employees began to hide their favorite scanners in nooks and crannies around the warehouse. That, in turn, often left the next shift even shorter on scanners. There wasn’t any trust in the workplace.
Supervisors sent in a steady stream of purchase orders for more scanners. The company’s total spend on new scanners crept up quarter after quarter. Eventually, the warehouse manager realized that they didn’t know how many scanners the company owned. They needed to adopt a more organized, lean approach to their warehouse operations.
The solution: an AssetTracer smart equipment management system
The clothing company installed AssetTracer systems to store and charge scanners in their warehouses. Instead of employees signing scanners out free-for-fall, they authenticated themselves at the smart panel and received a randomly selected scanner. That random distribution spread wear and tear across the entire pool of scanners. Then, if a worker didn’t return a scanner at the end of their shift, their supervisor would receive an email.
Management didn’t just dump the new system in the warehouse and let workers fend for themselves. Everyone needed to learn to trust the system.
The AssetTracer system wasn’t there to punish workers. It ensured everyone had the tools they needed to do their job right every day. The company took the time to train all of its warehouse employees and answer any concerns. They also established a clear policy so everyone understood their roles and responsibilities.
Scanner losses plummeted. The system also generated an automatic inventory of all scanners in the warehouse, so the clothing company, for the first time, got an accurate picture of their scanner inventory. That allowed them to slash their procurement budget considerably.
Trust the System and Lean Thinking Will Work
This company knew they couldn’t just dump technology on their staff and hope it worked. So instead, they took a lean approach to their process improvement and systematically addressed a problem in their organization. They aimed to reduce waste, decrease variance in how their people used company equipment and made the equipment transaction process transparent and automatic.
It made everyone’s lives easier and saved the company money. That took a solid foundation of trust.
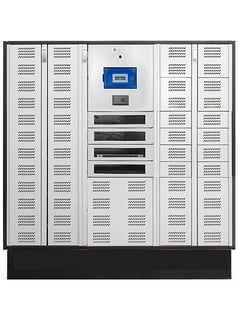
Want to find out if a smart equipment management system can improve your company’s lean performance?
Subscribe to our blog
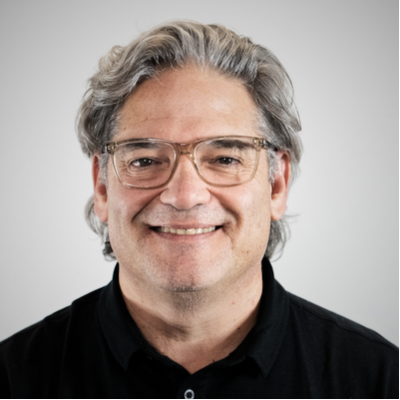
Jay Palter
Vice President of Marketing & Partnerships