By Jay Palter | February 23, 2024
Industrial automation has long been held up as an example of a competitive advantage that forward-thinking businesses deploy. However, as we move ahead into the challenging but transformative new world of Industry 4.0, it is now simply essential. Industrial automation is an indispensable tool for any business striving for sustainability and growth.
But this begs the questions: What exactly is industrial automation? And how will it shape the future of business in this new era of technological evolution?
What Is Industrial Automation?
Industrial automation is the networking and integrating of computers, information technology, robotics, and mechanical controls into industrial operations. Industrial automation aims to create efficiency improvement, generate new, meaningful insights through enhanced data collection, and elevate the quality of end products. In 2020, the global market for industrial automation was valued at approximately $175 billion. It is forecasted to expand at a CAGR of 9 percent through 2025. By the end of this period, the market is anticipated to approach a valuation of around $265 billion.
Industrial automation devices are managed via a computer system, which may be embedded within a single device or be a centralized, networked management system. Sensors linked to this computer track specific tasks, while actuators—either mechanical or electronic instruments—execute actions informed by collected data.
Industry 4.0: Tomorrow’s Competitive Landscape has Arrived
“Industry 4.0” is the nickname for the fourth major industrial revolution. Its hallmark is the use of smart automation systems and Internet of Things (IoT) devices to perform an ever-increasing number of industrial and manufacturing tasks.
Industry 4.0 businesses are also looking to connect automated systems to create more and better feedback loops that allow them to optimize every operation. Eighty-eight percent of businesses in the industrial sector have either started integration or automation efforts in at least one business unit or have plans to do so.
Key Elements of Industry 4.0
A few key design principles set Industry 4.0 technology apart from the previous generation of industrial automation.
Connected Information and Operational Technologies (IT & OT)
Information Technology (IT) helps process information for connected individuals and systems. Operational Technology (OT) focuses on the automation of physical processes. Before the advent of workflow automation, these types of systems functioned wholly separately. Today, discovering effective strategies for IT and OT integration represents a key avenue through which businesses can carve out new competitive advantages in the Industry 4.0 landscape.
Workforce Enablement
Industry 4.0 helps make many workers’ jobs easier and safer and supports the more complex and challenging knowledge work in industry. Automated systems can process data quickly but are not good at solving complicated problems or making tough decisions. People are still needed for these important tasks.
Learn More: How Smart Lockers Support Workforce Enablement
Decentralization
Smart automation systems equipped with AI capabilities can increasingly make important operational decisions independently without waiting for human intervention. This reduces the need for centralized management of day-to-day tasks. Additionally, this self-sufficiency enhances the effectiveness of an organization’s emergency response efforts, as smart systems can independently initiate shutdown procedures when needed.
Digital Transparency
Industry 4.0 automation enhances data gathering and analysis. Whether processed locally or remotely, new data can provide valuable insights for strategic decision-making. The deployment of compact, wireless Internet of Things (IoT) devices often expands the reach of automation into business operations previously inaccessible to monitoring and data-collecting systems.
Types of Industrial Automation
So, what does industrial automation look like in practice? Automation systems can be divided into three types: fixed, programmable, and flexible. All three types can be part of integrated systems.
Fixed Automation
Sometimes referred to as "rigid" or "hard" automation, fixed automation systems are designed to execute a single, repetitive task flawlessly over a long period. Once set up, these systems generally lack flexibility and require significant modification to perform a different task.
Ideal for high-volume, uniform production processes, fixed automation systems excel in performing monotonous tasks. An example would be a robotic arm that attaches a specific automotive component to an assembly line.
Programmable
Programmable automation systems are designed to carry out a specific task until a predefined condition triggers a switch to another task. This type of automation is particularly valuable for operations where the tasks may change within a well-defined scope.
A typical scenario involves an automated system that punches parts from a plastic sheet until reaching a set quantity. At this point, it ceases punching and activates a different mechanism to sort the parts. While these systems offer reprogramming flexibility for different tasks, changing their programming can lead to considerable downtime.
Flexible
Also known as "soft" or "smart" automation, flexible automation systems can alternate between tasks, similar to programmable automation. However, these systems have the added advantage of self-monitoring and adjusting their operations based on monitored conditions.
An example of flexible automation includes smart control systems, which can execute multiple tasks simultaneously based on inputs from humans and other systems. For instance, intelligent asset lockers can scan and verify the contents of returned equipment kits, alert maintenance personnel of needed repairs, and automatically reserve new kits for staff returning the equipment.
Integrated
Integrated automation systems consist of various components networked to function collectively. They can incorporate any previously mentioned automation types—fixed, programmable, or flexible—into a broader, cohesive system. An illustration of this would be a smart locker system combined with a real-time location tracking solution, enabling the simultaneous monitoring of equipment and personnel across a worksite.
Key Advantages of Industrial Automation
Understanding how automation can improve industrial operations will help you decide which solutions make the most sense for your business. Smart industrial automation systems offer:
Work Enhancement
They can operate faster and for longer than human workers. The speed workers don’t bind automated systems that can move. They also don’t require shift changes or lunch breaks.
Lower Costs
Industrial automation eliminates excess human labor. Per unit, production costs drop significantly.
Higher Quality
They are capable of more reliable, consistent performance than human workers. Automated systems don’t make mistakes when they get tired. They don’t forget important safety checks.
Better Safety
Eliminating human error in many industrial practices also improves worker safety. Automation can prevent day-to-day accidents, injuries, and catastrophic failures.
Potential Disadvantages of Automation
While there are numerous advantages to smart industrial automation, it can have its downsides. Before you undertake an Industry 4.0 digital transformation, take the time to familiarize yourself with the potential pitfalls that come with deploying new automation systems.
Need for Increased Network Security
Expanding networked automation within an organization introduces additional attack surfaces vulnerable to cyber threats. A breach in a seemingly minor device can give hackers a foothold to escalate attacks toward core systems with more valuable data. Understanding the risks of various automation systems is crucial for implementing the best possible network security program.
Worker Displacement
Industrial automation can pose more than just technical problems but also create human resource challenges. By design, automation replaces human labor. Human workers won’t disappear in the Industry 4.0 era but must be shifted into different, often higher-skilled, positions. This is a disruptive process for businesses managing these transitions and for individual workers who see their occupations transformed and often relocated. Implementing worker training and support programs is essential in ensuring that the transition to Industry 4.0 is smooth, secure, and beneficial for all stakeholders involved.
Higher Up-front Costs
Despite their potential for long-term cost savings, smart technology systems often incur substantial upfront investments. It's crucial to take your time selecting new automation systems. Instead, dedicate time to crafting a comprehensive migration strategy aligning with your business objectives. A well-thought-out migration plan will guide purchasing decisions, avoiding unnecessary costs, unsuccessful system deployments, and potential strife between management and employees.
Increased Maintenance and Technical Support
While automation technology is almost always more efficient than manual labor, the systems still require maintenance. Implementing an industrial automation system usually requires specialized maintenance and technical support practices.
However, that presents an opportunity to repurpose workers' roles affected by automation. Transitioning displaced employees into these more technically demanding positions addresses the need for skilled maintenance personnel and supports workforce adaptation and growth.
Learn More: Optimizing Asset Maintenance Management for Growth
Industrial Automation Is the Foundation of the Future
So, what is industrial automation? For many businesses, it will be the foundation on which they compete in the Industry 4.0 marketplace.
Mobile device management is an important aspect many businesses overlook in planning their digital transformation. Automated asset management can give you the competitive advantage to push your business into the Industry 4.0 era.
Talk to an expert and learn how smart technology can transform your business.
Subscribe to our blog
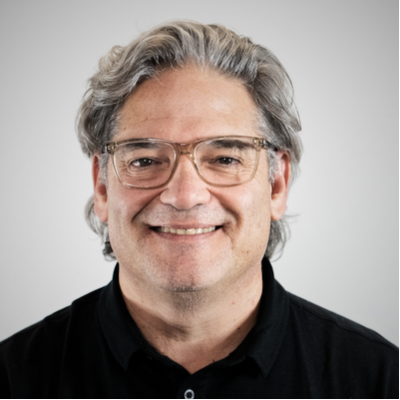
Jay Palter
Vice President of Marketing & Partnerships