By Jay Palter | December 7, 2020
Internet of Things (IoT) technology has had an impact on every business sector. However, IoT’s impact on the manufacturing and industry sectors has been notably large and came about quickly.
The pace of change is only expected to increase in the coming years. That isn’t something to be afraid of. IoT-enabled systems can improve many facets of industry and we should be looking for more operations that they can improve. Those could include:
- Employee workflows
- Product deliveries
- Maintenance
- Warehouse logistics
- Supporting day-to-day operations
What exactly are the benefits of IoT in industry? How can you apply IoT technology to your operations? Let’s dig deeper and find out.
How IoT Can Be Used in Industry
The Internet of Things is the latest generation of industrial, business, and consumer devices—the “things”—which now have a network connection. Formerly offline devices are now able to share information about themselves and their environment with connected people and computers. As the name suggests, the Internet of Things relies on expanded networking and interconnectivity, so network security is important for the successful deployment of IoT technology.
The catchphrase “Industry 4.0” has become a popular shorthand for IoT-enabled industrial business. A strong, steady expansion of Industry 4.0 business is expected in the years to come, with the global industrial IoT market expected to reach $949.42 billion by 2025. That represents a compound annual growth rate of 29.4 percent.
IoT technology is particularly good at integrating people-driven and machine-driven workflows in industrial settings. Done right, these integrated operations become more effective than the sum of their parts.
Smart Technology Can Transform How You Work
These integrated, IoT-driven systems are often thought of as smart systems. They track assets and collect data using attached sensors and software. Collected data is stored and processed in central computer systems, or sometimes in the devices themselves. These IoT-driven analytics can provide startling new insights into business operations.
Smart systems can be very effective at improving manufacturing and industrial processes. For example, smart asset management systems automate the tracking and distribution of handheld electronics that staff use during production and inventory management. These smart management systems not only oversee how handhelds are used, but they also connect directly into technical support, purchasing, and ERP systems to streamline how your whole company functions.
Top 10 Cost-Saving Benefits of IoT Smart Systems in Industry
What can you expect by implementing new smart management systems at your company? We see these as the 10 greatest benefits of IoT:
1. Increased Efficiency
IoT tools create many new opportunities to automate business processes that rely on human labor. These tools never get tired and can work across all shifts faster than human operators.
Many higher-skill activities can now be performed by smart IoT-enabled systems. This can include production line monitoring, end-of-run quality control, and equipment management.
2. Reduced Errors
Automating formerly manual tasks also eliminates the risk of human error, which is particularly important in manufacturing. A joint study by Vanson Bourne and GE found that 23 percent of all manufacturing downtime was caused by human error, compared to rates of as little as just 9 percent in other sectors. Reducing human error could mean reducing the chance of everything from small operational inefficiencies up to major catastrophic failures.
However, as you scale up your IoT deployment, it is also important to remove the risk of human error in IoT network security. Human error was shown to cause 52% of cybersecurity incidents in the manufacturing and industrial sectors in 2018.
3. New Insights
IoT tools can be used in dangerous or hard-to-reach locations not accessible to human workers. IoT sensors can be embedded right inside management systems and machinery. You’re able to manage work and monitor performance where you previously couldn’t.
The parts of your manufacturing process or overall business operations that previously occurred “in the dark” will be illuminated. You’ll have a more complete picture of how the different parts of your business function together, where future points of failure might be, and where you might be able to optimize performance.
4. Proactive Maintenance
Staff can report problems with electronic devices when they sign them out or return them to an IoT-enabled smart asset management system. The system can automatically notify support technicians, and then flag equipment on return for users to deposit it in specially designated maintenance lockers.
Aside from managing break/fix troubleshooting, technicians can also use the asset management system to proactively reserve equipment for scheduled maintenance or software updates. The system will lock down equipment so staff doesn’t accidentally sign it out.
5. Improved Compliance
Having an asset management program is often a requirement in many industry standards, such as ISO 27001. Automating asset management with smart IoT systems makes it simpler to ensure compliance with those standards. Retaining your standards certifications can often make the difference in landing new customers and government contracts.
ISO standards are all about linking assets to business risks and the workflows that surround those assets and risks in your wider organization. Basic tools such as spreadsheets are not good at tracking such an interconnected “ecosystem” of assets and processes. The software in smart asset management systems is an excellent tool for tracking every asset and their relationships to business processes in real time.
6. Reduced Expenses and Increased Revenue
Automating work so it is done faster and with fewer errors will both drive down costs and raise revenues. While automating manual processes using IoT systems requires an up-front investment in technology, those expenses are steadily recouped in saved labor costs over time.
The improved performance from automated smart technology can reduce other associated costs. For example, the tracking capabilities included in a smart asset management system greatly reduce asset losses, so your inventory replacement costs will go down over time too.
7. Better Worker Protection
IoT monitoring systems are also capable of tracking staff who are working alone or in dangerous locations. Employees wear wireless tracking badges on lanyards, clips, bracelets, or even sewn right into uniforms. When an employee triggers a safety alarm, management and security personnel are instantly notified so they can aid the employee.
In addition to helping protect those at-risk employees, safety logs can be pulled up during incident reviews to better understand how the accident occurred, the exact timeline of the accident, and your response. The real-time data recorded by the IoT system becomes an impartial eyewitness.
8. Optimization
One of the greatest strengths of IoT technology is its ability to collect and analyze data directly from your on-the-ground operations. These analyses can reveal trends you hadn’t seen before by just analyzing higher-level reports.
For example, a smart asset management system can collect data on how effectively different shifts and even individual workers use the equipment. Is your first shift constantly running a surplus of unused handheld scanners? Is the second shift always running short? Is that one first shift worker always late returning a scanner, slowing down the second shift’s start?
Once trends like these reveal themselves in IoT data analysis, you can take action to optimize how tasks, such as equipment distribution, are handled.
9. Efficient Integrations
Integrating IoT systems throughout your business gives you more flexible control over your entire production process. IoT systems connect staff, production equipment, and computer systems to make a high-performing, unified whole.
They bring data and work processes closer together. That means your production and business operations can respond to new insights faster and more often.
10. Facilitate Future Growth
Now is not the time to be left behind by the rest of the manufacturing industry. Tomorrow’s leading businesses will have built themselves on the foundation of IoT technology deployed today. By deploying smart IoT management systems, you’ll better prepare your business for whatever comes next.
IoT Creates Many Opportunities in Industry
IoT technology improves how people, formerly offline machines, and electronics all work together. It allows you to build a new organization that is greater than the sum of those different parts.
The pace of change is only going to increase in the manufacturing sector. Now is the time to think about how adding IoT tools will better prepare you for the future. There are many benefits to IoT in manufacturing and industry, and smart asset management systems are just one of the potential tools to consider.
Learn how to solve your organization's toughest security challenges, read our free guide, Physical Security 101, to learn everything you need to know.
Subscribe to our blog
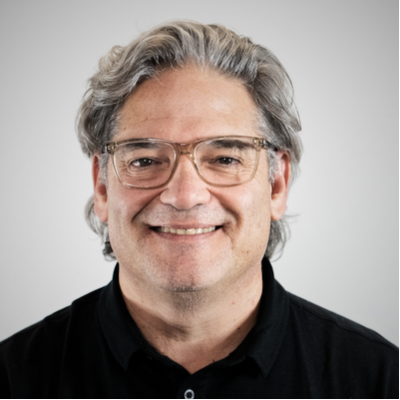
Jay Palter
Vice President of Marketing & Partnerships