By Jay Palter | May 23, 2024
If there’s one thing warehouse and facilities managers can be certain of, they will always be under pressure from business leadership to cut costs and boost productivity. There may be wider budgetary pressures, or their leadership might follow a continuous improvement business model. But whatever the reasoning behind that pressure, today, the key to identifying inefficiencies and eliminating waste lies in collecting and analyzing good data.
Effective forklift fleet management involves gathering, analyzing, and leveraging relevant fleet data to reduce expenses while improving productivity for both operators and vehicles. Access to comprehensive information brings new insights into fleet operations and helps answer critical questions, such as:
- How much is being spent on the fleet annually?
- Are the costs evenly distributed, or are some forklifts incurring disproportionately high expenses?
- Is the fleet correctly sized to provide sufficient capacity without excessive idle time?
- Are all operators and trucks hitting KPIs?
Despite these advantages, concerns over the cost and complexity of implementing comprehensive forklift fleet management systems have deterred some organizations from proceeding. However, the savings generated from these initial efforts can be reinvested to expand the program's scope and value.
This article explores how smart forklift fleet management systems work and the value they can provide to all levels of an organization.
Why use a smart forklift fleet management system?
Smart technologies can have far-reaching benefits beyond the specific workflows in which forklifts or other managed assets are used.Reduce fleet costs
When forklift usage data is accessible through an online reporting console, management gains an up-to-date, objective view of fleet costs. Vehicle replacements can be based on real-world servicing costs, not estimates, with the assurance that all lifts receive consistent, thorough maintenance. Analyzing the operating hours of each forklift across the entire fleet aids in decisions around fleet sizing and resource allocation.
With centralized management, unexpected charges can be minimized, and warranty repairs can be tracked to leverage coverage fully. This proactive approach shifts the focus from reactive repairs to disciplined preventive maintenance, boosting uptime and ensuring consistent service quality across the fleet.
While data collected during routine forklift maintenance offers valuable insights, forklift fleet optimization requires real-time data collection and analysis. You can achieve this through a number of means, including forklift key tracking or vehicle-mounted management systems that collect information directly from each forklift, regulate access through PINs or other identifiers, and transmit data to a central management system.
Improve productivity and compliance
A comprehensive fleet management system is essential for optimizing operations and should generate essential data on your forklift fleet and its use, including:
- Operators use hours—Monitors hours each operator uses specific forklifts to understand how work is performed and how active hours are distributed across your fleet.
- Battery or fuel status—Require operators to log power consumption when they sign out or return vehicle keys so you have up-to-the-minute records for which forklifts need refueling or recharging.
- Impact events and mechanical failures—Document incidents to refine forklift safety protocols.
- Equipment status—Track whether a vehicle is logged on, off, or in service.
When this data is aggregated across your entire forklift fleet, it provides a holistic view of fleet operations. That said, simply collecting data isn’t sufficient. It's crucial that this data is consolidated and presented in a format that aids decision-makers without overwhelming them. An overload of data can be as problematic as a shortage, potentially obscuring vital insights. For example, a good management system should help minimize equipment wear on individual forklifts by providing fleet managers with data to distribute use across the fleet and optimize resource utilization.
Generate new insights
Proper organization of forklift data is crucial for optimizing warehouse and material handling. Using a warehouse forklift management system, fleet managers primarily gather actionable insights during service events and through real-time forklift fleet monitoring. This not only reduces service costs but also helps in appropriately sizing the fleet and pinpointing underperforming vehicles and operators for targeted corrective actions.
These systems also enhance productivity by making forklift downtime more predictable through regular planned maintenance and impact monitoring. Effective resource management increases vehicle utilization rates, and tracking operator performance ensures that productivity targets are consistently met. Ongoing monitoring also supports continuous improvement business plans, like Lean or Six Sigma.
Technologies for forklift fleet management
Fleet managers can use several different technologies in a unified smart fleet management system alone or in conjunction.
Forklift telematics
Forklift telematics uses wireless technology to collect and transmit data from individual forklifts to a central management system. These systems monitor engine hours, fuel consumption, forklift maintenance alerts, and impact events. This real-time data allows fleet managers to identify operational inefficiencies, schedule preventive maintenance to minimize downtime, and ensure compliance with safety standards.
RFID and barcode scanning
RFID (Radio Frequency Identification) and barcode scanning are vital tools for accurately tracking the movement of inventory and equipment within a warehouse or storage facility. Managers can efficiently monitor their location and usage by attaching RFID tags or barcodes to pallets, boxes, or individual items. This technology enables seamless data collection for accurate inventory counts and helps prevent misplacement or theft of goods. It also ensures that forklift operators follow proper processes for material handling, contributing to safety compliance.
GPS tracking and geofencing
GPS tracking provides real-time visibility into the location of each forklift in a fleet, helping managers identify route inefficiencies and optimize utilization. Geofencing adds another layer of security by creating virtual boundaries around specific areas. When a forklift crosses these boundaries, managers receive instant alerts, allowing them to prevent unauthorized usage or quickly respond to potential security breaches.
Key management & asset management systems
Key management systems integrated with asset management systems provide secure, controlled access to forklifts and other equipment. By ensuring that only authorized personnel can operate machinery, these systems enhance accountability and reduce the likelihood of equipment misuse or damage. The system logs each access event, providing a detailed audit trail for compliance and investigation purposes. This information can also reveal operator performance trends, helping managers make data-driven forklift operator training and resource allocation decisions.
Cloud-based fleet management software
Cloud-based fleet management software centralizes all data related to forklift operations, providing a unified platform for managers to oversee the entire fleet. This software facilitates real-time data analysis, reporting, and performance tracking, offering insights into maintenance schedules, operator productivity, and safety compliance. Because it's cloud-based, managers can access critical information anywhere, enabling prompt decision-making. It also simplifies the integration of telematics, RFID, GPS tracking, and other data sources, giving a holistic view of the fleet's performance.
Maximize Warehouse Productivity with Smart Forklift Key Management
Manage your forklift fleet more efficiently with our smart key management systems for warehouses and distribution centers.
Best practices for modern forklift fleet management
Here are some proven best practices fleet and warehouse managers can adopt for effective forklift fleet management. Regardless of fleet size or complexity, these guidelines can simplify the lives of managers and operators alike.
Maintain robust policies
Document clear and easy-to-follow policies covering all aspects of fleet use and management. Well-structured policies streamline communication and enforcement, significantly reducing fleet managers' administrative workload.
Optimize fleet usage
Manual fleet operations often need to be more efficient as the fleet grows. Adjust checklists or logging procedures to keep forklifts fueled or charged and in working order. For instance, drivers must log fuel levels and damage upon return, ensuring vehicles are maintained properly and consistently.
Use process control checklists
Implement mandatory checklists for vehicle key sign-outs and returns to encourage accountability. Requiring drivers to complete a checklist before receiving or returning keys ensures that they log mileage, report vehicle damage, and take responsibility for their assigned vehicles.
Rotate forklift sign-outs
Operators often have a preferred vehicle, but allowing them to select the same forklift repeatedly can lead to uneven wear and tear across your fleet. Develop a system that rotates vehicle assignments or uses lifecycle management technology to automate the process. This approach distributes mileage more evenly and balances maintenance schedules.
Focus on preventive maintenance
Don't wait until significant repairs are needed. Establish a preventive maintenance schedule for all fleet vehicles. Regular maintenance is more cost-effective over time, mitigating potential issues and maintaining overall vehicle health.
Optimize fleet size
Strive for balance in fleet size. Maintaining excess forklifts strains your budget, and maintaining too few will impact operations. Maintain enough vehicles to handle emergencies and unexpected downtime while avoiding excess capacity.
Track everything
Data collection is key to optimizing fleet utilization and making informed purchasing decisions. Although specific metrics will vary based on fleet composition, here are some data points most every fleet manager will want to monitor:
- Fuel usage—Track fueling dates, quantities, and costs.
- Vehicle utilization—Record sign-outs for specialized forklifts and other facility vehicles.
- Driver performance—Log all license and certification expirations accident details, including dates, times, locations, and nature of the incident. Record the personnel involved and any insurance claim information.
- Maintenance—Monitor scheduled and unscheduled repairs, noting work performed, maintenance dates, parts used, and associated labor costs.
- Purchasing and leasing—Maintain accurate records of contract and warranty details for all purchased or leased vehicles.
Technology makes forklift fleet management better
If you need help with how to begin improving your forklift fleet management, Real Time Networks offers several solutions that can help. Our smart key and asset management systems enable fleet and warehouse managers to track their forklifts more efficiently, cost-effectively, and safely.
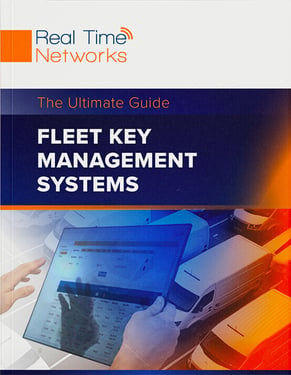
Get The Ultimate Guide to Fleet Key Management Systems
Explore how these systems work and how they can benefit your operations by streamlining fleet key distribution, enhancing security, and offering valuable insights through data analytics.
Subscribe to our blog
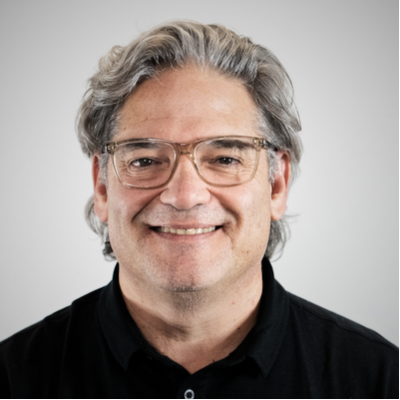
Jay Palter
Vice President of Marketing & Partnerships