By Jay Palter | March 4, 2024
IoT is the Internet of Things, the latest generation of business and consumer equipment connected to the Internet. These devices can communicate with each other or central computer systems and your personnel in your workplace.
It sounds like IoT devices would be a perfect tool for industrial automation. But is that always the case?
IoT and smart management systems can be cost-effective solutions for managing how your industrial equipment, your staff, and their IoT devices work together. There are many advantages of IoT and this digital-native approach to business. But there are some traps you can fall into during your transition if you’re not planning carefully.
How We Can Use IoT in Industry—2024 and Beyond
The worldwide market for the industrial Internet of Things (IoT) was estimated to be worth $394.0 billion in 2023, with projections from the Grand View Research firm suggesting an annual growth rate of 23.2% through 2030.
Why the massive uptick in interest? Broadly, the main reason is that networked IoT devices establish feedback loops. They can monitor industrial performance and send data to central computer systems for analysis. Then, they can carry out instructions that are returned. Industrial IoT solutions are self-monitoring, self-adjusting types of smart technology.
The most common activities we can expect to see smart IoT systems perform in industry include the following:
- Data collection
- Performance monitoring
- Actionable analytics
- Remote management
It is important to highlight that while industry will become increasingly automated going forward, people won’t disappear from the workplace. IoT’s greatest strength is augmenting how people work, not replacing them. However, the roles in an industrial workforce will change, and business leaders must ensure their labor forces can still effectively work in these new, automated environments.
To that end, three trends are on the horizon for industrial automation and IoT that you should be aware of:
What is Industry 4.0?
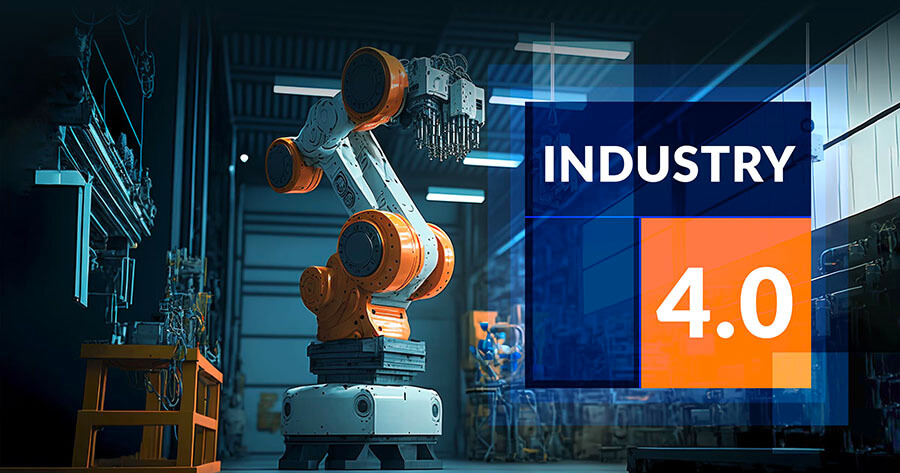
Industry 4.0 is the fourth industrial revolution. It is characterized by smart manufacturing, Internet of Things (IoT) technology, cloud computing, and big data strategies. Companies embracing the Industry 4.0 approach fuse all those technological capabilities into their workflows. This integration enables a closer link between workers and their machinery and management systems
AI & Machine Learning
Smart IoT systems gather data that AI and machine learning programs can analyze to spot trends and opportunities that human workers might miss. These services can also improve their operations based on feedback from people and IoT devices. This is key to improving:
- Warehousing operations
- Asset tracking
- Inventory management
- Supply chain monitoring
- Supply/demand forecasting
Predictive Maintenance
Companies can use IoT and AI together to take care of their production tools, mobile devices, and IoT endpoint devices more effectively. Combining IoT and AI management systems helps you identify maintenance support issues before they cause problems.
This proactive maintenance approach significantly reduces downtime. Additionally, IoT and AI technologies facilitate easier analysis of performance trends. That helps you refine maintenance schedules and informs your future procurement plans.
Expected Outcomes When Industrial Automation and IoT Work Together
Industrial enterprises integrating smart technology into their workflows can expect improvement across several areas. It's not necessary to commit to a full-scale overhaul immediately. You can expect to see these five benefits even in smaller-scale IoT investments:
Efficiency Improvement
Smart systems function at a significantly higher speed than manual labor. Their non-stop operation can reduce downtime closer to zero. They don’t need breaks or holidays or need to take sick leave. Work can proceed uninterrupted, even during periods of reduced workforce availability.
They also support seamless shift transitions since they’re always on and available. For example, by facilitating the exchange of mobile devices from workers in one shift to the next.
Fewer Errors
Automated systems are far more precise than human workers. Humans can get tired, make mistakes in production, or misenter data. Electronic systems don’t suffer from these problems. IoT systems can also capture a significantly higher volume of data with more detail than manual methods. This wealth of data enables more thorough and detailed analyses, and in turn, better decision-making.
Easier Regulatory Compliance
Many businesses must meet specific industry or quality standards in their production processes, which IoT industrial automation can support. Automation's capacity to minimize production errors enables organizations to comply with strict regulatory requirements.
Better Working Conditions
By adopting industrial automation and IoT systems, we can shift the most dangerous and labor-intensive tasks away from human workers, decreasing workplace accidents. This shift reduces the likelihood of workers' compensation claims and production setbacks and reduces stress for both the workforce and management.
Wireless IoT solutions are particularly beneficial in environments that are difficult or costly for human workers to access. In industrial settings, this could mean automated guided vehicles (AGVs) operated remotely for safe material handling and process automation in hazardous areas.
Furthermore, IoT systems are adept at managing monotonous tasks that are tedious for humans, such as logging and tracking assets in management systems. This automation of routine duties enables employees to dedicate their efforts to tasks requiring human insight and skill, where they are most valuable and find the most satisfying.
Cost Reduction
The up-front costs of deploying an IoT smart management system are quickly recouped by the reduced labor necessary to maintain operations. These savings grow yearly as you use insights from IoT data to optimize workflows.
Smart management systems also help you drastically reduce losses and inventory shrinkage. For example, smart asset management systems can almost completely eliminate industrial handheld equipment loss.
The asset management system immediately alerts supervisors when workers do not return a device on time. Promptly starting a search significantly boosts the likelihood of retrieving missing equipment. Supervisors can review transaction reports to spot concerning patterns early on and address them before they escalate into major issues.
Challenges to Watch Out for When Implementing Industrial IoT Solutions
Some organizations try to jump headlong into end-to-end transformative IoT deployments without properly considering the challenges they might face. Taking on too much too soon can delay, or even stop, their industrial automation and IoT rollouts.
No matter which system you’re deploying for which use case, these are the three most common challenges that you need to plan for in your deployment plan:
Unexpected Up-front Costs
Although IoT solutions offer significant cost savings over the medium and long term, their deployment is still an expensive upfront capital investment. Some careful planning is essential to prevent delays and extra expenses during deployment.
Many worry they’ll need to go through a complex project management process, but that is not often the case. Often, simply collecting insights from operational staff and involving all stakeholders so everyone is on the same page is enough to streamline IoT deployments. Collaborating with a seasoned solutions provider well-versed in the intricacies of the technology platform you intend to deploy also helps ensure a smooth and efficient deployment.
Physical & IT Security
Thanks to the deployment of newly integrated IoT sensors, many previously offline industrial equipment are now connecting to the internet for the first time. That introduces a host of new security threats and instabilities to business networks.
The inherent value of IoT devices makes them potential targets for internal and external theft. It's important to assess which devices are most vulnerable. Mobile electronics that play a pivotal role in the transition to Industry 4.0 require rigorous security solutions and careful management to safeguard against loss, theft, and misuse.
It is crucial to involve your IT department early in the planning stages of new IoT automation projects to ensure comprehensive protection.
Integration & Management
Although automated systems take over numerous tasks that human employees once handled, they still require proper management and upkeep. Businesses looking to deploy mobile electronics to their workforce as a part of their IoT automation initiatives often need to pay more attention to how much management is required to maintain an inventory of such devices. Without a coherent strategy for device management, there's a risk of inadvertently creating even more manual work for your employees, not less.
Deploying automated management systems will require staff to undergo training to adapt to new tools and workflows. Traditional operation procedures may become obsolete as IoT technology redefines how we carry out routine work. Neglecting to adequately prepare your team for the changes brought about by Industry 4.0 could negatively impact your organization's operational efficiency and overall performance.
A Clear Vision Forward, but Still Many Decisions to Be Made
The future of industry lies in IoT and other smart technology. It is not a question of whether expanding your industrial automation and IoT systems is a good idea. It is only a question of how you get results most effectively. Smart storage systems can solve the challenge of managing how your staff and mobile IoT electronics will need to work together.
Talk to an expert and learn how smart technology can transform your business.
Subscribe to our blog
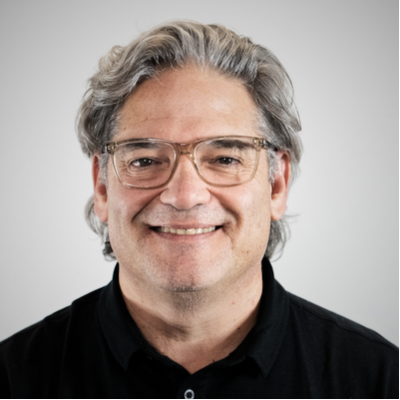
Jay Palter
Vice President of Marketing & Partnerships