By Jay Palter | May 19, 2021
Real Time Results — A Series of Confidential Case Studies
This case study is part of an ongoing series that gives readers a behind-the-scenes look at some of the most challenging and sensitive business problems Real Time Networks has helped solve. The clients are confidential. The results are real.
The food service industry has long been known for consistent but tight profit margins. Food service businesses have to be serious about efficiency. A couple of years ago, a multinational food service company was particularly concerned about the efficiency of their warehousing and shipping operations. Specifically how they managed their expensive handheld scanners.
This company sells and distributes kitchen equipment and food products to restaurants, hospitality businesses, and healthcare and educational institutions around the world. At the time their annual profit margins were good for their industry at just below 3.5%. But that was still a very tight margin.
Managing Scanners Was a Serious Problem
At one of the company’s 400,000 square foot distribution centers they had only bothered tracking handheld scanners using pen-and-paper logs. Managing the scanners had gotten so complex that during first shift the company had pulled a supervisor from other work just to be a scanner inventory manager. But then on second shift, as one of their floor managers put it, “it was a complete free for all.” Another frustrated senior source at the company added, “This resulted in high labor costs and many ‘not logged transactions.’”
Worker walk times and wait times were too high. So were scanner loss and repair rates. They had invested over $250,000 in their current generation of handhelds and accessories, and they were still buying dozens of replacements every quarter. The problem wasn’t showing up only on financial reports either, it was affecting warehouse workers day-to-day.
Scanners were so mismanaged and unready that workers were grabbing as many spare batteries as they could to get through their shift. This was leaving so many batteries uncharged that the following shift employees were left with dead scanners. So they learned to start taking extra spares, and the cycle repeated.
Taking Control of Inventory
At that point the center Shipping Director at the food service company decided to find a better asset storage solution for their scanners. They were intrigued by the AssetTracer intelligent storage system and reached out to Real Time Networks to see what the options were for customizing it for use at their warehouse.
Their RTN representative suggested they start by outlining the specific workflows that they wanted an asset storage system to manage. Together the consultant and the Shipping Director did some fact finding within the warehouse and came up with a list. The storage system would need to:
- Authenticate every worker that signed out or returned a scanner
- Restrict access in the storage system to only the individual asset being signed out
- Require workers to log error codes when returning scanners
- Verify returned scanners and report unreturned scanners to managers at the end of shifts
- Ensure stored scanners were fully charged
Putting a Plan into Practice
The RTN consultant pulled together a proposal for deploying AssetTracer systems at the warehouse that could handle every one of these concerns. The plan involved deploying asset lockers for scanners at all of the start-of-shift locations within the warehouse. The Shipping Director got the green-light for purchasing. Their leadership was impressed with how customizable both the AssetTracer security cabinet hardware and the management software tools were. The integrated RTNHub portal would be able to automatically manage some of the tricky workflows that other systems on the market weren’t flexible enough to accommodate.
Automated email and SMS alerts could be designed so supervisors knew in real-time if scanners were missing. Integrated charging ports ensured that idle scanners and spare batteries were always ready. And Real Time Networks could design quick checklists that workers had to complete at the cabinet’s access control terminals to log any maintenance notes for technicians.
Real Time Networks configured the modular storage lockers and the software to optimize warehouse workflows. The system went live once the lockers were deployed, and the software configured.
Steady Efficiency Gains
Warehouse staff were impressed with the new systems. The RTN sales executive said, “When the install was complete, the customer had great feedback. Staff were ecstatic they wouldn’t have as much paperwork to complete. And they liked how good the cabinets looked.”
The results in just the first year were impressive. Operating efficiency improved dramatically. The company saved over 1,000 hours in staff time eliminating unnecessary wait and walk times in only a few months. Lost handhelds were eliminated. And they were able to cut 20 scanners from their equipment replacement schedule, saving the company over $40,000 over the following four quarters.
Warehouse managers admitted that some workers were resistant to learning the new system at first. But after seeing how the system worked adoption picked up fast.
Then following some worker suggestions, the company began storing more than just individual scanners in the AssetTracer system. They began storing tool kits, along with scanners in locker compartments. The system was able to restrict these customized tool kits to just the staff allowed to access them. And they were available across shifts.
Now this multinational food service company is seeing steady efficiency gains in their distribution center as scanner availability is improved. The AssetTracer system didn’t just improve how their scanners were stored, it improved how their entire distribution center performed.
Want to learn how your business can benefit from intelligent asset storage?
Contact Real Time Networks Today for a Free Consultation
Subscribe to our blog
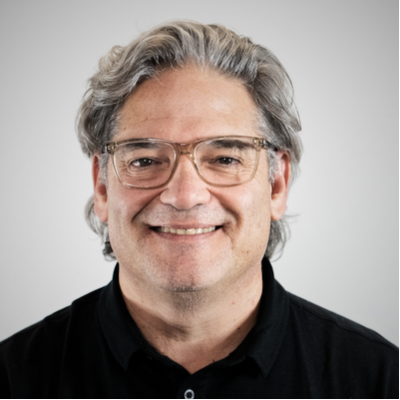
Jay Palter
Vice President of Marketing & Partnerships