By Jay Palter | May 24, 2023
Every year, corporate security departments have new threats added to the lengthy list they already have to deal with. New insider threats, dangerous technologies, disruptive market forces, social changes, the list goes on. All while contending with budgets constantly under scrutiny from C-suites that want to shrink cost centers as much as possible. No wonder corporate security management teams are searching for any advantage they can get.
Many security departments have turned to RFID smart lockers as potential solutions. Thanks to networks of wireless RFID sensors and smart security management technology, these locker systems can take over most of the heavy lifting that comes with administering large bases of corporate security equipment, medical supplies, and other consumables used by security teams. They can even help manage the workflows and security protocols within which your officers use that equipment.
This article explores corporate security management's challenges in equipment management and highlights how smart management systems help overcome those challenges.
The Costs & Challenges of Manual Corporate Security Management
Maintaining a corporate armory at full readiness is expensive. It is even more expensive when you rely on human labor for all administrative work. The direct costs are obvious, but lurking behind those are many indirect costs corporate security leaders might not have considered.
To get perspective on the problem, it is worth first understanding what exactly manual security equipment management costs your business. We can break costs down into three categories:
- Material costs
- Personnel costs
- Regulatory costs
Material costs
The larger your company’s inventory of firearms, radios, mobile devices, PPE, first aid kits, and other gear, the more manual management is required. For example, inspections and servicing both take time. So does managing those service schedules and tracking equipment used during operations.
Since tracking individual weapon and equipment use is very time-intensive, many security teams just service their gear on a set schedule. But that approach only makes sense for equipment that will degrade at a constant rate, which might not be true for mobile electronic devices, which receive software updates on their manufacturers’ schedules.
On the other hand, your high-use equipment may need repairs more frequently than what you have scheduled. But you might not know if you don’t have real-time insights into its status and health. That is why it is essential to maintain live usage and transaction records so you can customize schedules.
Personnel costs
While equipment costs add up quickly, personnel-related costs are often the largest ones corporate security teams must contend with. Consider all the management tasks a security manager must perform. At the most basic level, they might include:
- Logging new inventory assets
- Updating existing records
- Managing transactions
- Auditing existing storage
- Recovering lost or missing gear
- Ordering replacement gear
- Filing departmental reports
- Filing state and federal compliance reports
And then there are inevitable human errors. Even small ones can generate large downstream problems. For example, suppose one of your security officers returns their weapon and equipment belt but forgets about their radio. It might just be sitting at their desk or in their locker, but your other officers need it available for the next shift. And eventually, they will spend valuable work hours hunting for a vital piece of equipment that could have just been automatically and accurately tracked in the first place.
Regulatory costs
Security teams are often mandated to track when personnel use less-than-lethal (LTL) weapons, like pepper spray and tasers. In addition, asset tracking on opioid painkillers in first-response kits may also be necessary to comply with narcotics regulations.
Error-prone, manual tracking exposes security teams to too many security risk management violations and fines. For example, an incorrect transaction time or unentered signout name may prevent them from conducting necessary security audits on the chain of custody for firearms or controlled substances.
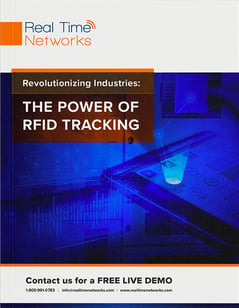
Discover the Power of RFID
See how RFID tracking systems work, how they’re used in different industries today, including healthcare, and some best practices for adapting them to your center’s care practices.
Benefits of Using Smart Equipment Management Systems
So what exactly can smart locker systems do to make life easier for corporate security personnel? Here are ten key benefits these tools offer security teams.
Usage tracking
RFID sensors in lockers enhance control over equipment transactions. Radiofrequency identification (RFID) content surveillance systems can scan each kit component even through hard cases.
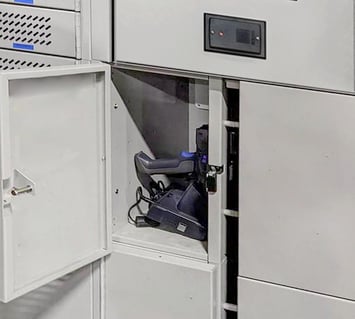
Automated transactions
During normal operations, when security personnel need something from your equipment tracking system, all they have to do is quickly authenticate themselves at the attached smart terminal, tap the inventory menu to confirm what they need, and then grab it from the locker that opens for them. You can configure the terminal to accept whatever credentials you want, from PIN codes for low-security environments to access cards and biometrics. The smart terminal can then present the user with procedural checklists to improve accountability and usage logging.
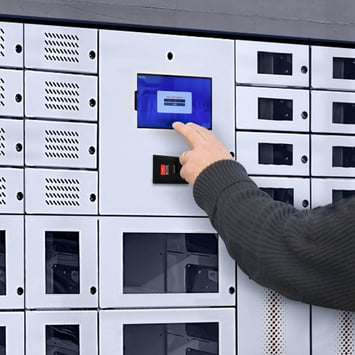
Better lean management
Corporate security systems provide so much more than just monitoring the physical materials they store. They provide insights into the workflows within which those items are used. The tools these systems provide help you control where, when, and how your security personnel use assets.
Better tracking will help you automate and standardize important processes so that work is carried out consistently, reliably, and with good feedback when errors occur. For example, you’ll know immediately if any security officers start their shifts without their essential gear.
Learn why lean companies are using smart equipment management systems.
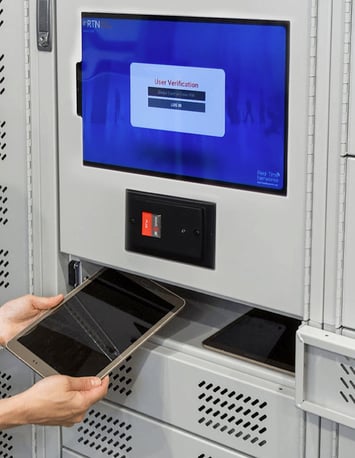
Secure, customizable storage
Companies have different physical security equipment storage needs. For example, a multinational pharmaceutical company will want to store different equipment for personnel with very different duties and patrol patterns from a regional manufacturing business. In addition, those organizations operate on different schedules, have different security risk assessments, and worry about entirely different emergencies.
So while they both may want smart equipment management systems, those systems need to function very differently. For example, advanced smart lockers have a modular design, so you can stack together different-sized compartments to store the gear, LTLs, and PPE your team needs in the space you have to work with.
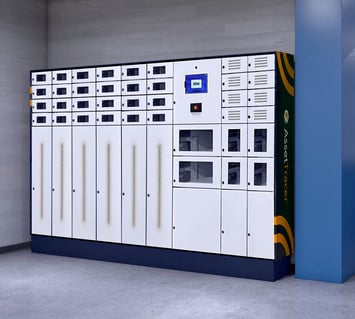
Real-time insights
Smart locker systems are fully digital. You get instant insights and alerts on what you care about most from content surveillance sensors in lockers compartments and the management dashboard. If someone tries to gain access to the gear you haven’t authorized, you’ll know instantly without any risk of compromise. If someone doesn’t return sensitive assets on time, you’ll know immediately too.
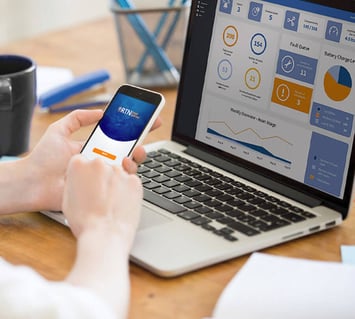
Reporting
The data the equipment management system collects feeds into a central dashboard your managers can access on authorized PCs and mobile devices. That improves corporate data security.
Transaction times, who signed out which items, when they returned them, whether they were late, and any equipment faults reported, all of this information and more is compiled into reports you can access in just a few clicks.
You can set alerts to go to email automatically, so you know the moment there is a problem. For example, if a security officer hasn’t returned a handgun or a radio at the end of their shift.
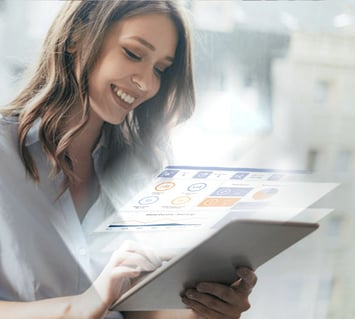
Remote management
Larger enterprises can network their various on-site equipment management systems together. For example, they can have one at headquarters and give more at regional offices nationwide. They all network together, share user access privileges, and track equipment use.
Smart system reporting can also reveal patterns you might not have noticed otherwise. For example, security officers at all five regional offices may see the same shirt battery life printed with the latest batch of radios your equipment manager ordered.
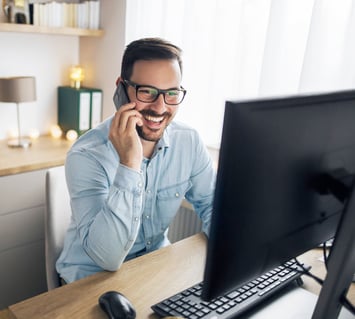
Consistent access
Smart lockers make inventories more available than human equipment managers ever could. Smart technology never gets tired, doesn’t leave when a shift ends, and never has to call out sick. Smart equipment management systems give security teams control over who can access which gear and when around the clock. You can restrict access by individual, location, or job type. You can configure lockers only to release sensitive assets, like radios and firearms, to properly registered and certified personnel.
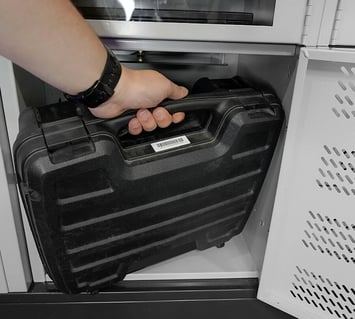
Universal authentication
Smart equipment management systems replace error-prone manual tracking with smart access control terminals that record every transaction. In addition, they support a range of authentication types.
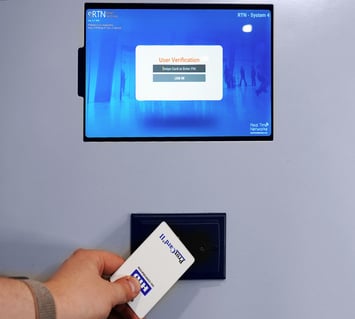
Error-free asset tracking
Since transactions are automated, your security officers can sign out or return equipment 24 hours a day. They don’t need to wait for an equipment manager to be on duty.
And since you can build quality control checklists into transactions, you still exert the necessary checks and balances on sensitive equipment use. Reminders on the smart terminal screen can help prevent officers from accidentally forgetting kit components when responding to an incident.
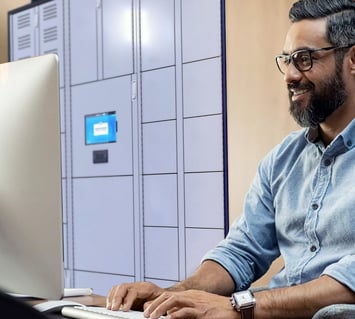
Smart Equipment Management Leads to Efficient Security Operations
Corporate security management teams increasingly turn to automated equipment management systems to manage their electronics, firearms, and other security equipment. Corporate security budgets are only getting tighter, and these teams need ways to save on labor costs without compromising effectiveness. Implementing better equipment management is one of the best ways to achieve this goal.
See what RFID can do for the security of your organization.
Subscribe to our blog
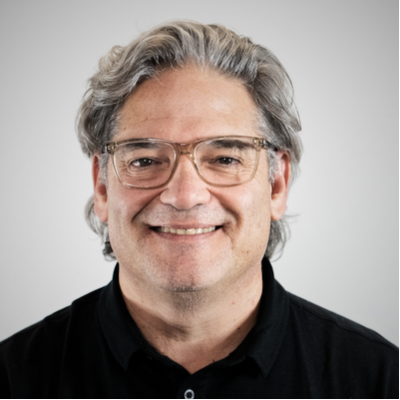
Jay Palter
Vice President of Marketing & Partnerships