By Jay Palter | May 29, 2024
Physical asset management definition
A physical asset is any tangible item a company owns and utilizes to generate value. These assets include infrastructure, buildings, equipment, vehicles, and land. They are crucial to a company's operations and require effective management to ensure longevity and sustained value.
Some examples across different sectors include:
- Asset management in Manufacturing — Machinery, equipment, and tools.
- Asset management in Energy — Power plants, pipelines, and transmission lines.
- Asset management in Transportation — Vehicles, vehicle keys and fobs, and tool kits.
- Asset management in Manufacturing — Buildings, forklifts, handheld devices.
Physical asset management involves controlling and monitoring assets throughout their lifecycle within an organization. It involves structured processes for planning, acquiring, maintaining, operating, and disposing of these assets in the most efficient and cost-effective manner possible.
Physical asset management strategies
Two main approaches exist for companies to manage their physical assets: Reactive and proactive asset management.
Reactive asset management—This approach focuses on repairing or replacing assets after they break down. While it may seem straightforward, reactive management is often costly and can result in unplanned downtime, lost revenue, and safety hazards. Effort is shifted from planning to response.
Proactive asset management—In contrast, proactive asset management involves continuously monitoring assets, predicting potential failures before they occur, and performing preventive maintenance to avoid disruptions. This method reduces risks, enhances reliability, and maximizes the value of physical assets.
Learn More: Optimizing Asset Maintenance Management for Growth
What is the goal of physical asset management?
The primary goal is to maximize the value of physical assets while minimizing the risks associated with their ownership and operation. An effective asset management strategy ensures that physical assets are:
- Available when needed — Ensuring assets are ready and accessible when required.
- Reliable and fit for purpose — Maintaining assets so they perform reliably and meet operational needs.
- Cost-effective to operate and maintain — Managing assets in a way that optimizes operational and maintenance costs.
- Compliance with regulations and standards — Ensuring assets adhere to relevant laws, regulations, and industry standards.
- Safely and sustainably managed — Operating assets in a manner that prioritizes safety and sustainability.
The physical asset management lifecycle
Effective physical asset management requires taking an organized approach. Understanding and managing the entire asset lifecycle is essential if you want your physical asset management program to enhance operational efficiency properly. When businesses lack a clear understanding of their assets, use, and overall life cycles, they risk falling into reactive maintenance habits. That can quickly lead to accelerated asset depreciation and higher maintenance costs. Conversely, embracing lifecycle management—from procurement to disposal—enables teams to make informed decisions and ensure exemplary asset efficiency. In other words, more proactive management.
Planning
The asset lifecycle begins when your team identifies a need for a new asset. During the planning stage, the asset manager and procurement team collaborate with various departments to determine:
- The specific asset required
- The purpose it will serve
- How it will improve operations
- Available budget
- Asset health forecasting and estimated depreciation over time
At this stage, assessing how the asset aligns with overall business goals and its potential to enhance operational efficiency and revenue generation is crucial.
Procurement
Once the planning phase identifies the required asset, the next step is commissioning or purchasing it. This involves:
- Defining the asset specifications
- Conducting market research to shortlist suppliers
- Negotiating pricing and delivery options
- Finalizing the purchase
Operation and maintenance
This is the longest stage of the asset lifecycle, where the asset is deployed and operational. Throughout this phase, it is important to track the asset’s performance and maintenance requirements using a comprehensive maintenance strategy and quality software. Effective maintenance planning reduces downtime, minimizes repair costs, and maximizes asset longevity. Businesses without a maintenance plan are likely to see a decline in asset reliability and performance.
Disposal
At the end of its lifecycle, the asset is removed from service and disposed of through selling, repurposing, recycling, or discarding. The asset manager determines the most effective disposal time by considering environmental regulations and data security issues. If the asset needs replacement, the lifecycle returns to the planning stage for an alternative asset.
Learn More: Managing Asset Lifecycle Better With a Smart Asset Management System
What are smart lockers?
Smart lockers streamline many of the daily workflows of a physical asset management program. These systems comprise modular locker compartments, wired and wireless sensors, and a smart access control system. Together, these components monitor and manage asset health through a secure web dashboard.
Learn More: [Download] Ultimate Guide to Smart Lockers
Secure storage lockers
Smart lockers come in various sizes and often feature a modular design, allowing customized configurations to meet specific storage needs. These lockers can include integrated power and data ports for electronic devices and offer climate-controlled or refrigerated compartments for sensitive assets such as medications or biological samples.
Smart locker systems for asset accountability
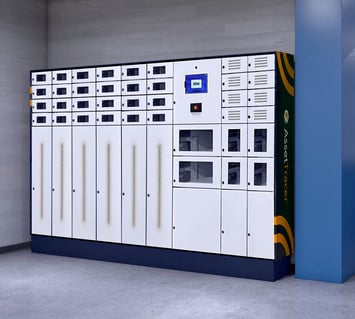
Smart access control panels
Each smart locker system includes an access control panel for user authentication. These panels can include various forms of authentication, including PIN code keypads, biometrics, or swipe cards. Advanced tablet touch screens provide enhanced capabilities and workflow support.
The access panel can be configured to prompt users for the specific device they need, unlocking only the designated compartment. Additionally, it can present checklists during sign-out or return, enabling the collection of essential information about the asset or its intended use.
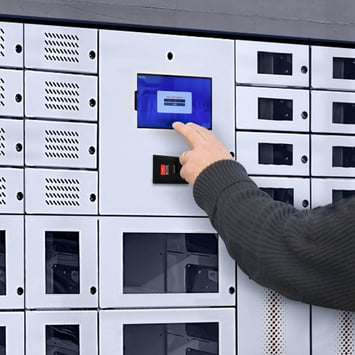
Asset surveillance
Beyond secure storage, smart lockers can incorporate RFID sensors, scales, and other monitoring devices within locker compartments. This feature, known as asset surveillance, allows the system to automatically verify that users are taking and returning the correct items and provides status updates. For example, if each component in a kit is tagged, RFID sensors can confirm whether all components are present when the kit is returned.
Learn More: [Definition] What is Physical Asset Surveillance?
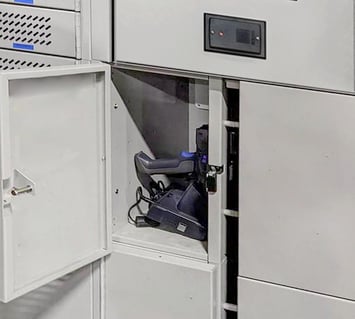
Management software dashboard
The software management dashboard is the backbone of the smart locker system. It offers real-time monitoring of locker usage and allows administrators to adjust user access privileges, review alerts, and generate customized reports. This interface ensures comprehensive oversight and efficient management of all stored assets.
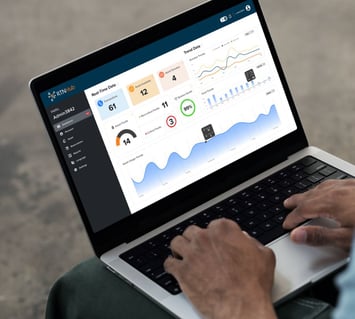
Core processes of physical asset management supported by smart lockers
Smart lockers can improve your asset management program in several ways.
Asset lifecycle management
Smart lockers enhance asset lifecycle management by tracking and monitoring assets from acquisition to disposal. The system records every interaction with an asset, including check-outs, returns, and maintenance activities. This data helps forecast maintenance needs, plan replacements, and ensure assets are utilized effectively throughout their lifecycle. Additionally, integrated sensors and monitoring devices provide real-time updates on asset health, usage patterns, and potential issues, enabling proactive management.
Learn More: 10 Proven Strategies for Effective Equipment Lifecycle Management
Increased accountability and control
Smart lockers increase accountability and control by ensuring only authorized personnel can access specific assets. Each locker interaction is logged, creating an audit trail that tracks who accessed which asset and when. This feature discourages misuse and loss of equipment as users know their actions are being monitored.
Learn More: Equipment Tracking Systems: Choose the Right Tech for Loss Prevention
Inventory management
With smart lockers, inventory management becomes more efficient and accurate. RFID sensors, USB connections, weight scales, and other monitoring devices within the lockers automatically track the presence and status of assets. This automation reduces the need for manual inventory checks and minimizes errors. Real-time data on asset availability helps managers maintain optimal inventory levels, ensuring that essential tools and equipment are always ready for use.
Learn More: Top 10 Equipment Inventory Management Practices to Follow
Maintenance management
Smart lockers streamline maintenance management by tracking the usage and condition of assets. The system can be programmed to alert managers when an asset reaches a certain usage threshold or shows signs of wear and tear reported by users. Maintenance schedules can be integrated into the locker management system, ensuring regular checks and servicing are performed. This proactive approach reduces downtime, extends the lifespan of assets, and maintains operational efficiency.
Track your assets and manage their lifecycles with AssetTracer
Get the peace of mind that comes from knowing your most important assets are accounted for at all times.
Benefits of asset management programs
The importance of asset management cannot be overstated. Developing a rigorous asset management program supports a range of critical business initiatives. Here are the key benefits:
- Improved operations — Enhanced control over workflows involving your equipment boosts overall organizational performance.
- Better risk management — An asset management program's tracking and auditing processes aid in informed decision-making regarding equipment purchase, deployment, and field handling.
- Loss prevention — Continuous monitoring of equipment transactions and usage ensures a complete 'chain of custody' record. This facilitates quick investigations and the recovery of missing assets.
- Cost reduction — An asset management program ensures the effective use of equipment. It guarantees that the correct, functioning assets are always available, and scheduled condition checks ensure timely maintenance, preserving the value of each asset.
- Supports overall business growth — By reaching across the entire organization, an asset management program fosters collaborative workflows, connecting business units more closely. This alignment ties organizational operations more effectively to business goals.
- Encourages accountability — Training personnel to care for and use assets responsibly cultivates a broader culture of responsibility and accountability within the organization.
Smart lockers have a broad range of applications
Real Time Networks’ AssetTracer smart locker system has proven incredibly versatile, solving various unexpected challenges for our customers.
Airplane safety
Airlines must ensure that large, sharp knives used in food preparation do not inadvertently end up on airplanes. We partnered with a major airline to embed RFID tags in knife handles. Using the AssetTracer locker system, they receive a live, automated confirmation that all knives are returned after use, ensuring none are taken onto airplanes.
Learn More: Optimizing Aircraft Maintenance Through Effective Tool Management
Complex asset logging
A police force required a solution to track multiple components of a radar kit stored inside a hardened carrying case. We designed asset lockers to detect each component’s RFID tag through the case. The RTNHub system reads each asset individually and alerts commanding officers if any kits are returned with missing parts.
Customizable workflows
A municipal EMT department needed a reliable way to track medications in their ambulances. To address this, we developed a checklist application for their touchscreen panels. EMTs are prompted to confirm the correct dosage amounts when signing out and returning medicine bags. This system not only ensures accuracy but also updates the RTNHub for better order and recall management.
Learn More: Healthcare Equipment Management: Improving Operations with RFID Technology
Laptop repairs
Smart lockers can be programmed to trigger specific alerts when items are placed in them. Several businesses have implemented an inventory management system using AssetTracer to notify IT when electronics need troubleshooting. Typically, one locker in each module is designated as a ‘repair locker.’ When an item requiring repair is deposited, it triggers a real-time alert to IT, notifying them of the new job.
Learn More: Smart Locker Solutions for Laptops, Mobile Devices and Keys
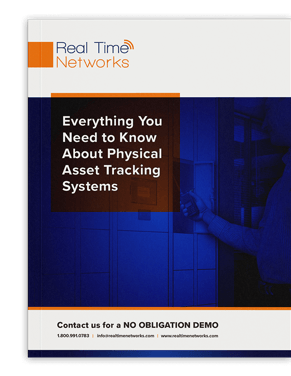
Protect your Organization's Assets Effectively
A smart asset management system can make your organization more productive, efficient, and accountable.
Subscribe to our blog
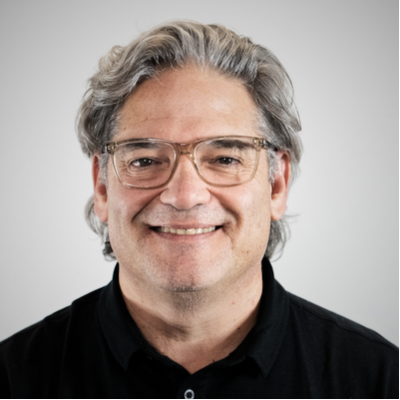
Jay Palter
Vice President of Marketing & Partnerships